Sustainability is a question of commitment for us.
Always one step ahead: climate neutrality by 2050
The HAI Group is committed to reducing emissions in accordance with the latest scientific findings, contributing to limiting global warming to a maximum of 1.5°C and becoming climate neutral by 2050.
Science-Based Targets are specific emissions targets set by companies that are based on scientific recommendations. This commitment is a further step by our HAI Group as a pioneer in the field of sustainable aluminium products.
All-round sustainability:
The HAI aluminium cycle
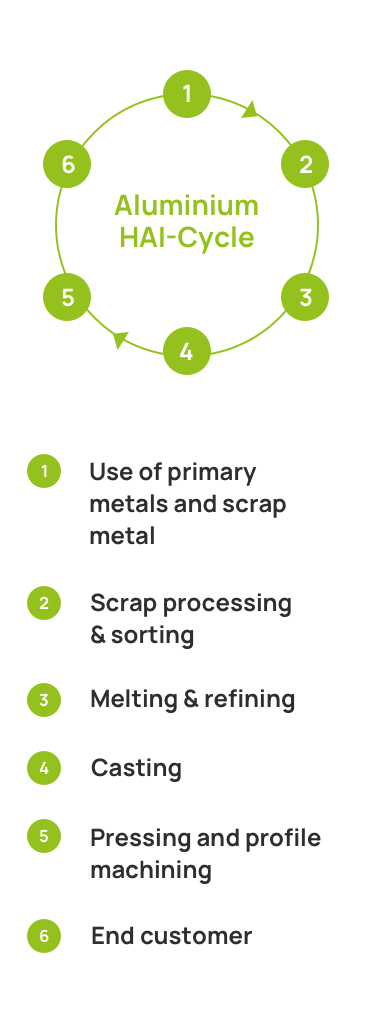
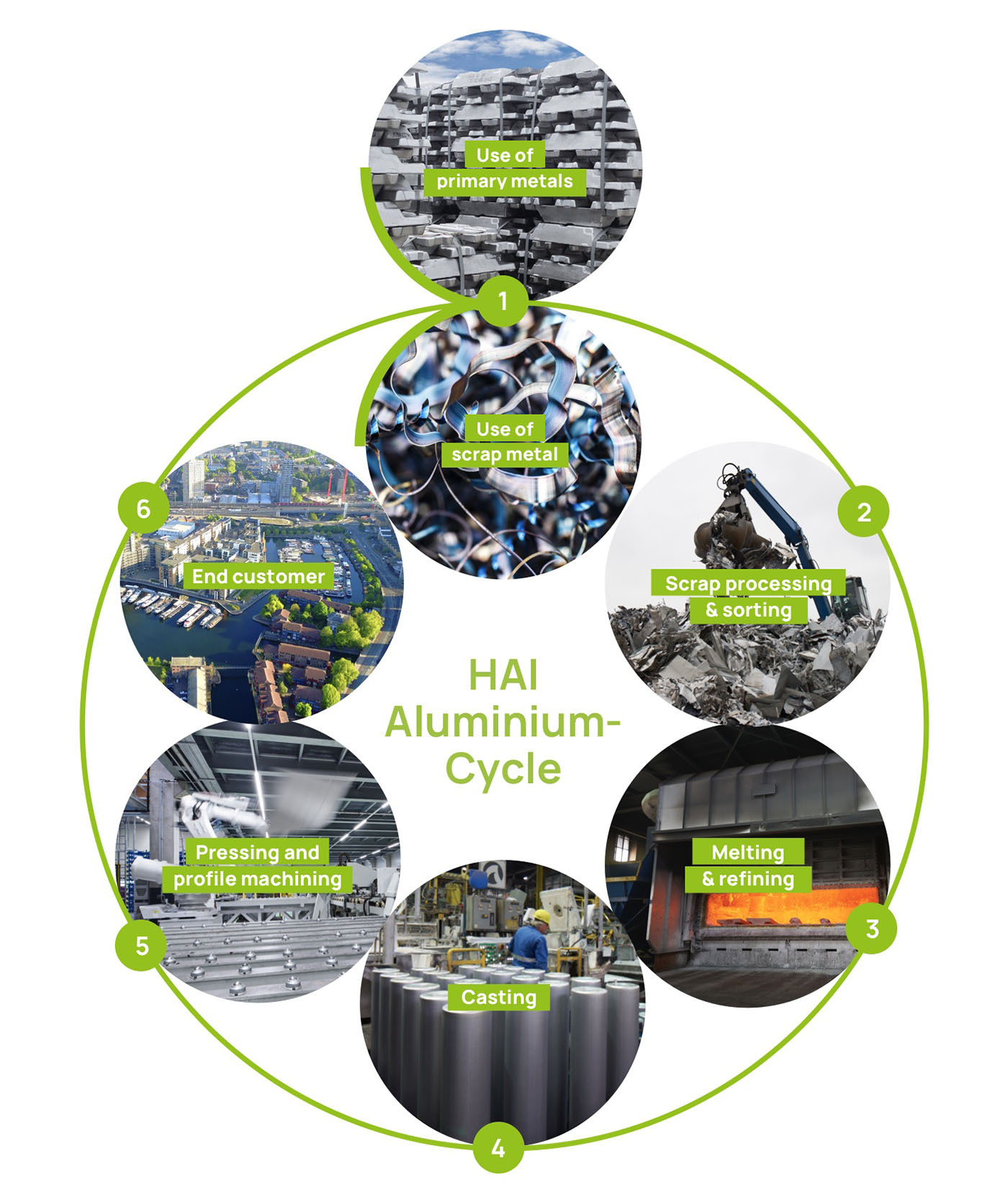
Sustainable corporate management as the basis
“Recycling and the sustainable manufacturing of our products that is associated with it have become key issues for the future. For us it’s important to ensure that scrap aluminium from all our product segments is efficiently recycled so as to increase our recycling rates and consequently make a contribution to climate neutrality and the circular economy.”
Markus Schober, COO HAI Group
The pillars
of our sustainable actions
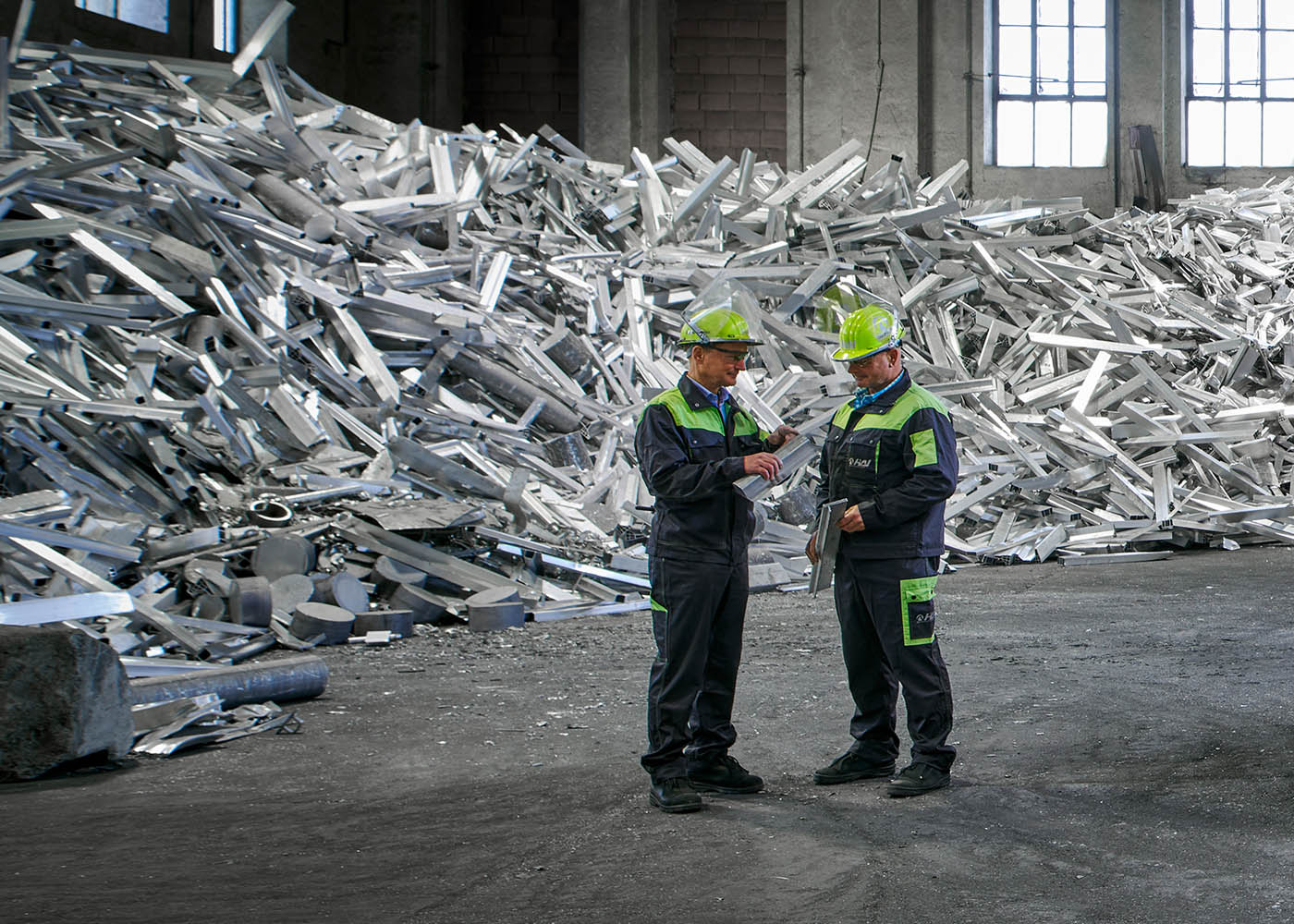
Efficient, consistently applied recycling as the key to success
Most emissions within the aluminium industry are caused during the production of primary aluminium. Increasing the recycling rate will enable the CO₂ footprint of the entire sector to be significantly reduced. At HAI we can reduce our energy consumption by up to 95% and our CO₂ emissions by up to 80% by using recycled aluminium rather than primary metals.
An extraordinarily high recycling rate such as that achieved by HAI is only possible by using a wide variety of types of scrap, and by having an extensive knowledge of the material together with an appropriate production process, not to mention our employees’ years of recycling expertise. So in order to ensure the best possible use of scrap we have in recent years made considerable investments in production systems, furnace technology, waste material management, and the processing of scrap.
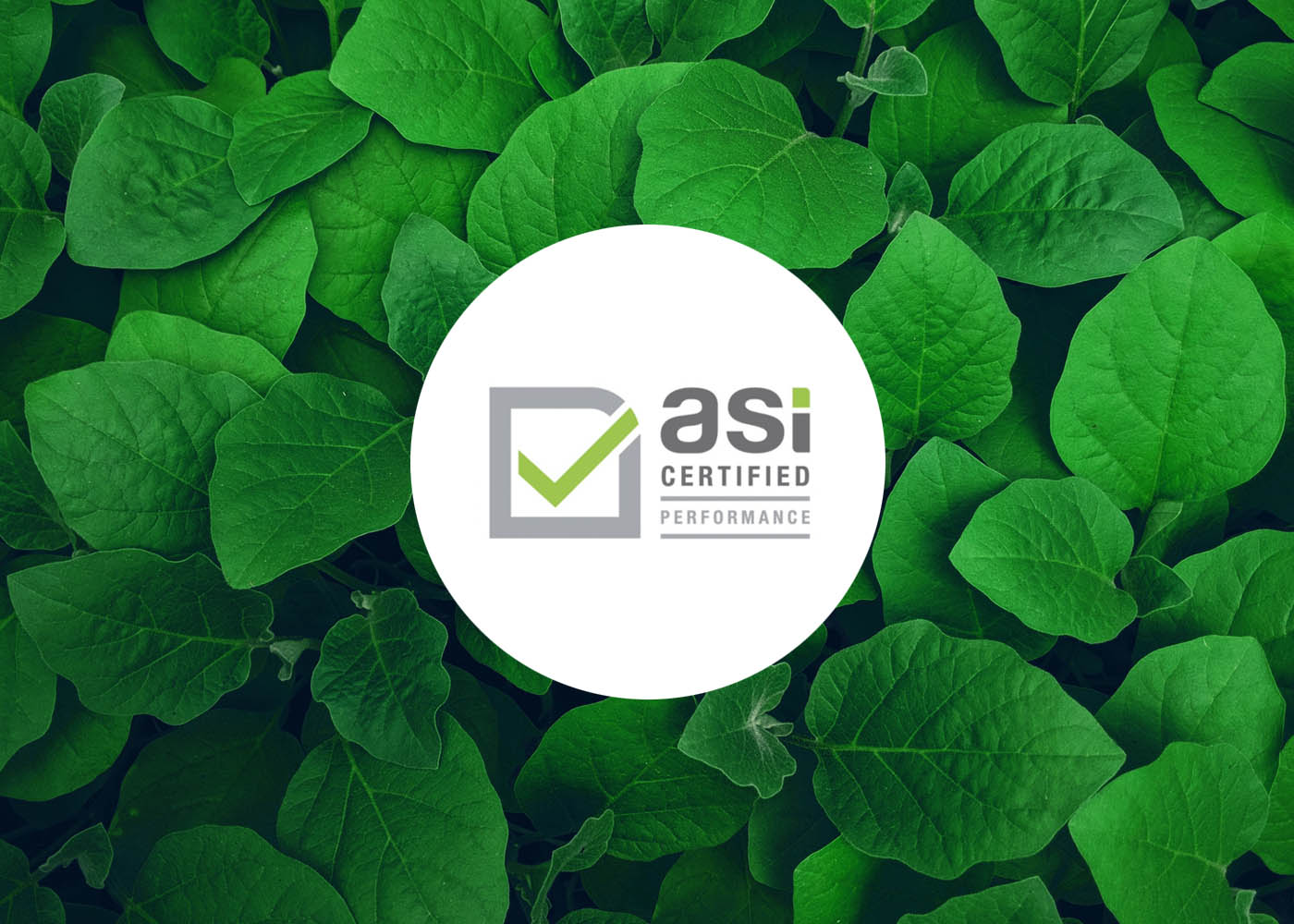
Excellent, resource-efficient production facilities
Sustainability goes back a long way at HAI and it’s also reflected in our certified production facilities and the traceability of raw materials. We are convinced that good energy efficiency and resource-efficient production methods will promote the development of new technologies and procedures. For example, the Casting division at Ranshofen achieved Performance Standard certification under the Aluminium Stewardship Initiative (ASI) in March 2020, followed by the Santana (Romania) site in September 2020. Extrusion and Processing in Ranshofen and Extrusion in Cris were certified in 2022 as well. Our aim is to unite the entire value creation chain for aluminium in a sustainable way and to make the production of aluminium products a “clean business” from start to finish.
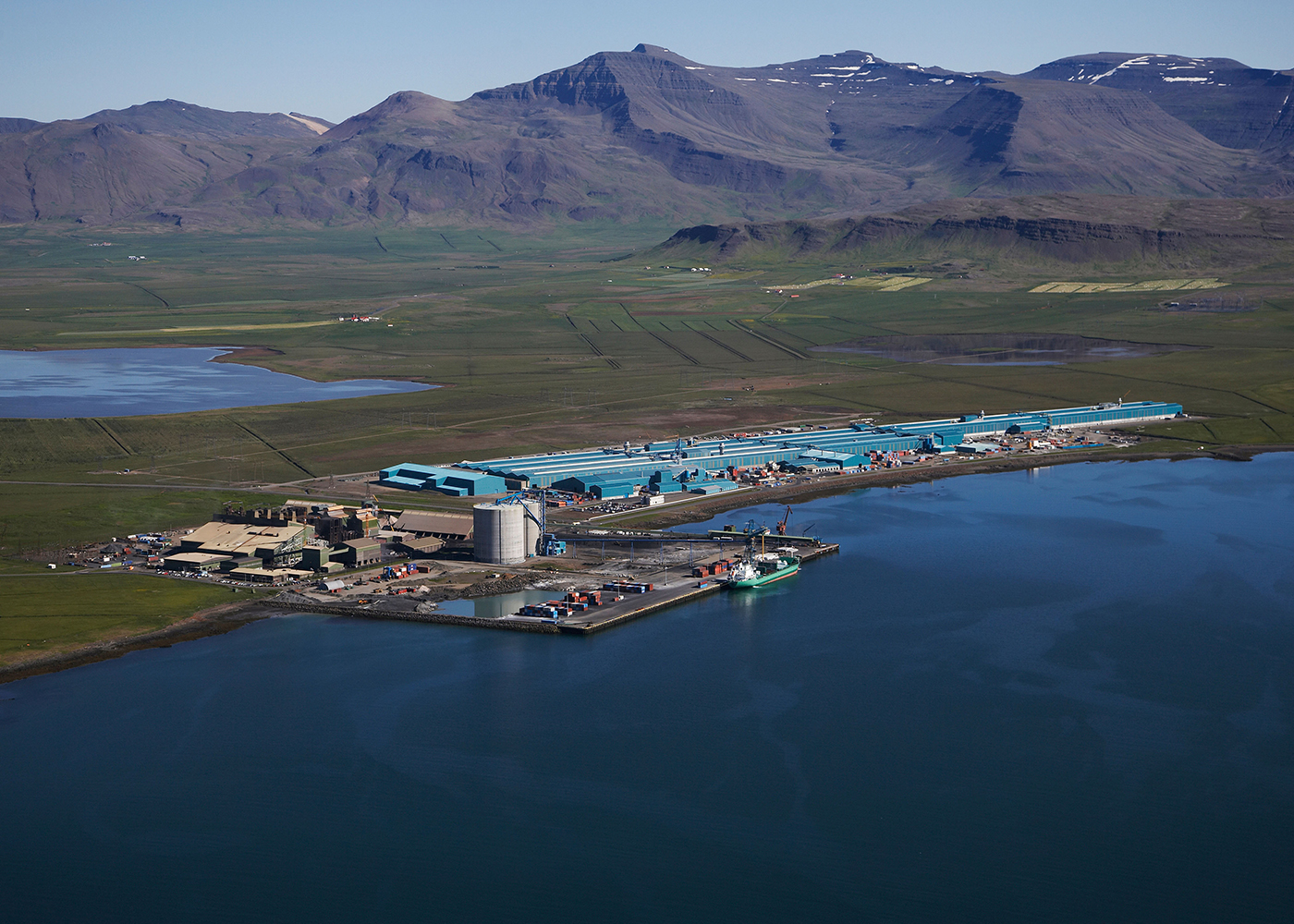
Green too as regards raw materials
Here at HAI we act extremely responsibly when purchasing “green primary aluminium” or when procuring sustainably produced billets for making profiles.
Supply contract for Natur-Al™ products
That’s one of the lowest Co₂ footprints in the world for this metal. The entire Co₂ footprint per tonne of aluminium is four tonnes. That’s less than a quarter of the average for the sector as whole.
For HAI as a recycler and recycling smelter, the CO₂ content of the primary aluminium that is obtained has a massive impact on the overall footprint. This supply agreement is a clear statement that the HAI Group is not cutting any corners when it comes to its sustainability commitments. Thanks to the combination of Natur-Al™ aluminium and our recycled materials we can produce billets and rolling slabs using less than two tonnes of CO₂ₑ per tonne of metal. This underlines our efforts to do our bit to improve the future for everyone.
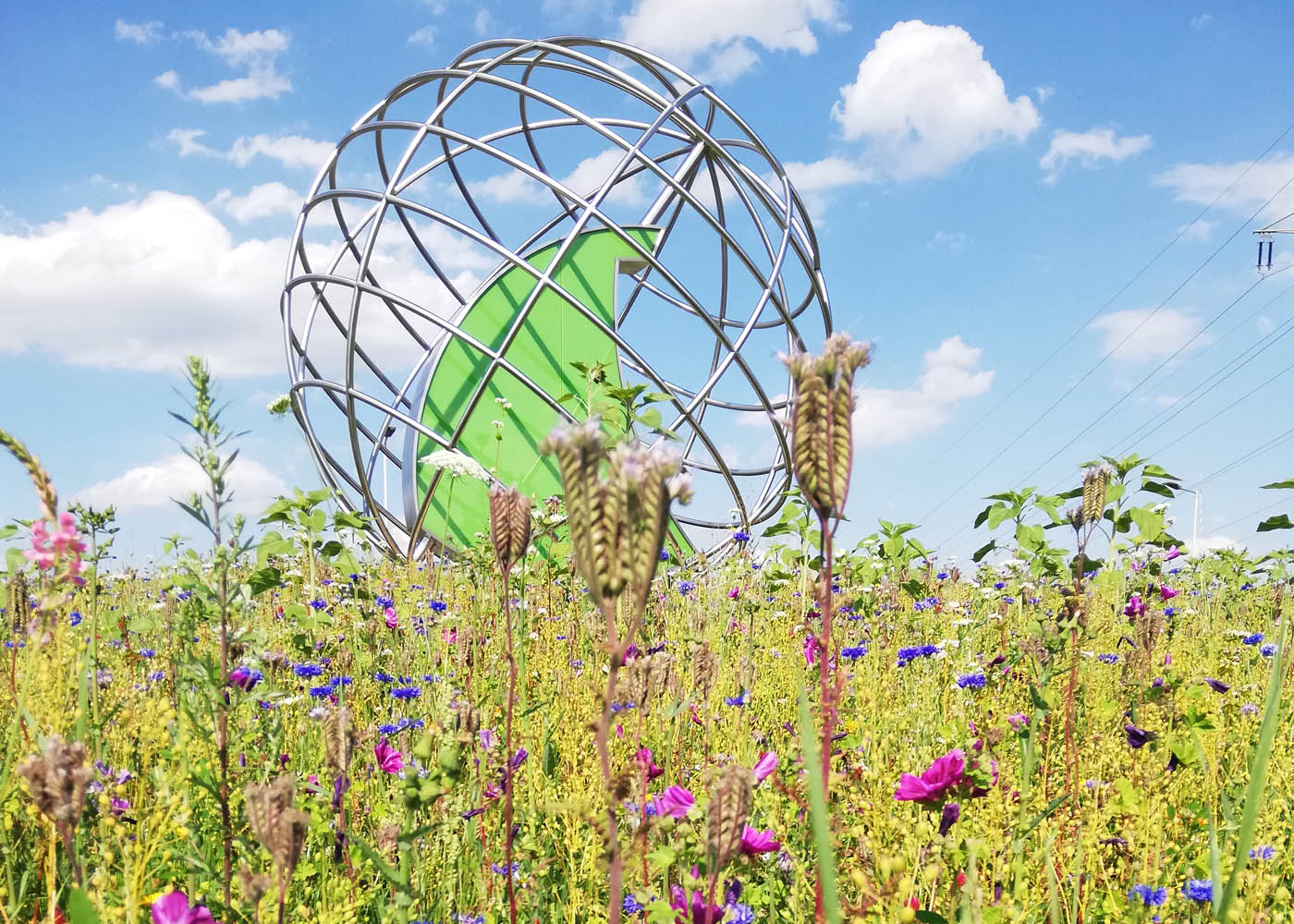
Consistent green electricity strategy
By buying 100% CO2-neutral hydroelectricity HAI is committing itself to the green energy transition in this area too.
Simply converting to green electricity has enabled us to significantly improve our overall CO2 footprint. In 2020 we managed to save about 3,400 tonnes of CO2 just at the Soest site, and as much as 17,600 tonnes at Ranshofen. As a way of visualising this, the annual CO2 saving of 21,000 tonnes of CO2 is equivalent to the footprint of 3,000 people (in Austria each person produces about 7 tonnes of CO2 every year).
Since January 2021, both sites in Romania are also supplied with 100% CO₂-neutral electricity generated from hydropower and wind power. The majority of the corporate group has thus completed the energy transition.
At the Ranshofen site, we operate one of the largest PV self-consumption plants in Austria with an area of 9,300 m² and a total output of 2.15 MWp. In 2023, the system produced 1,588 MWh of green electricity from solar energy, which corresponds to around 4.6% of energy consumption at the Ranshofen site. This enabled us to save around 300 tons of CO₂ and around 200,000 euros in electricity costs in 2023.
The photovoltaic parks in Sântana and Cris were completed in 2024. The raw material (SustainAl 2.0) was supplied by Sântana and the aluminium profiles were extruded in Cris. With a total output of 5.5 MWp, we cover around 25 % of the site’s energy requirements in Sântana. In Cris, with a total output of 5.2 MWp, we cover around 27% of the site’s energy requirements. Since the systems in Cris were commissioned in spring 2024, we have achieved a total yield of 880 MWh as well as a saving of ~418 t CO2 and 571 equivalent trees planted. In Sântana, we have achieved a total yield of 1,100 MWh and a saving of ~534 t CO2 and 730 equivalent trees planted since commissioning.
There is also a photovoltaic system in Soest since 2023 with a total output of 0.650 MWp. The system generated around 251 MWh in 2023, covering 1.56% of total consumption.
New e-fuel stations are also an important part of our sustainable strategy: once the production of components for battery trays for the EQC (Mercedes-Benz’s first electric-powered SUV) is running at full speed, the mobility revolution will also become a reality at HAI within the company itself. There are already several e-cars in use within the car pool at HAI, including two Mercedes EQCs. At the company’s site in Ranshofen there are also nine charging stations for company cars and for visitors with electric cars.
All these activities are part of a large-scale initiative within the HAI Group, which is addressing the issue of sustainability throughout the aluminium industry’s entire value creation chain.
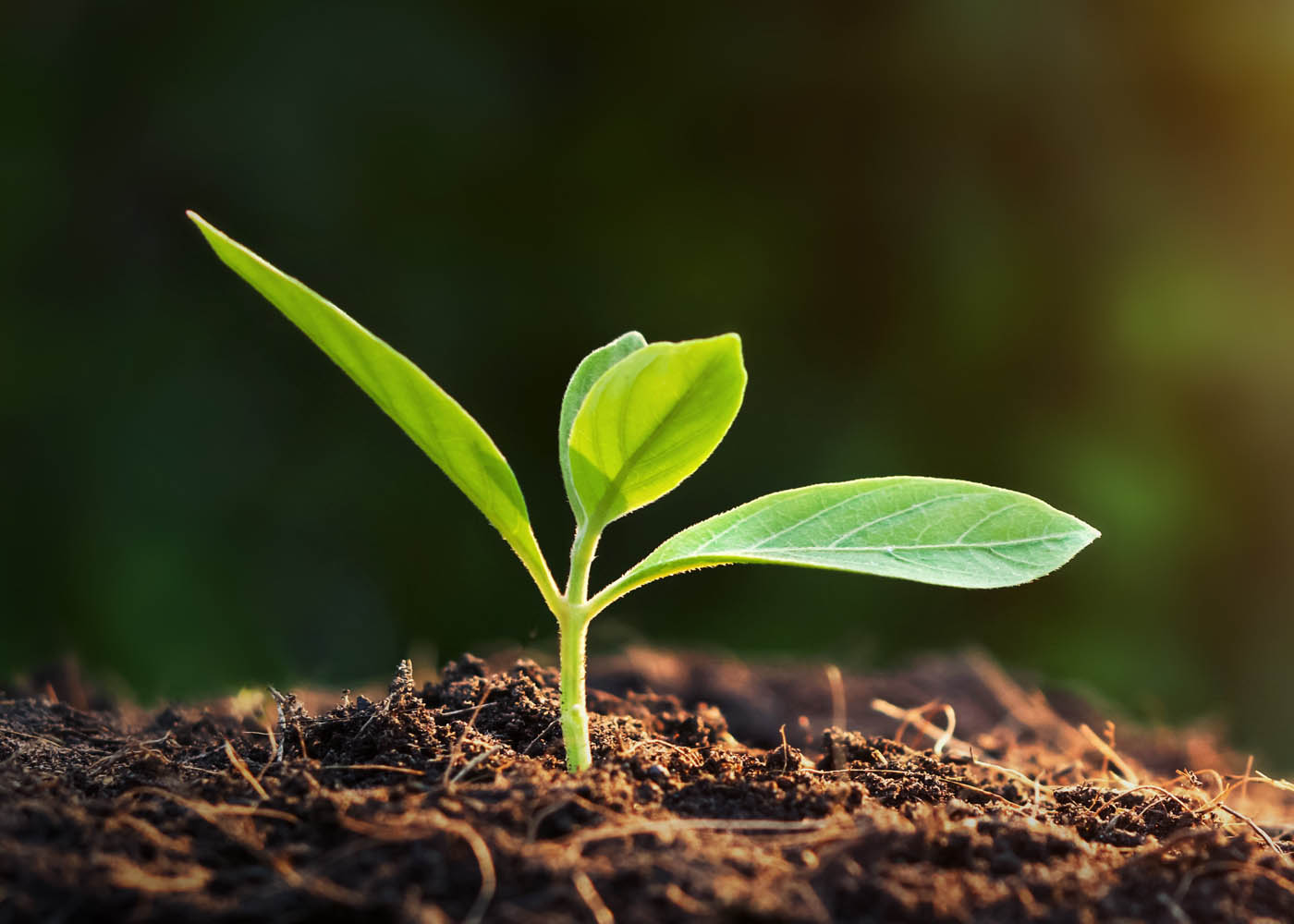
Using the best technologies to achieve even greater sustainability
Sustainable energy management is also a top priority at HAI. We believe that it is crucial for a company within the aluminium sector to take a responsible approach to its high energy requirements. That’s why at HAI all the processes and procedures are subject to continuous improvement.
In terms of the use of energy and energy consumption this means:
- Optimization of the billet heating system
- Reducing electricity consumption by improving the efficiency of the ventilator drive systems
- Replacing existing lighting with LED lights
- Reducing the amount of gas that is used by replacing cold air burners by self-recuperative burners
- Using heat recovery at the compressor station
- Reducing the consumption of diesel by regularly replacing old vehicles
- Shorter door-open times at the furnaces
- Electromagnetic stirrers for improved heat transfer
These measures are reviewed and evaluated as part of regularly carried out energy audits, and any new recommendations that are made as a result are implemented.
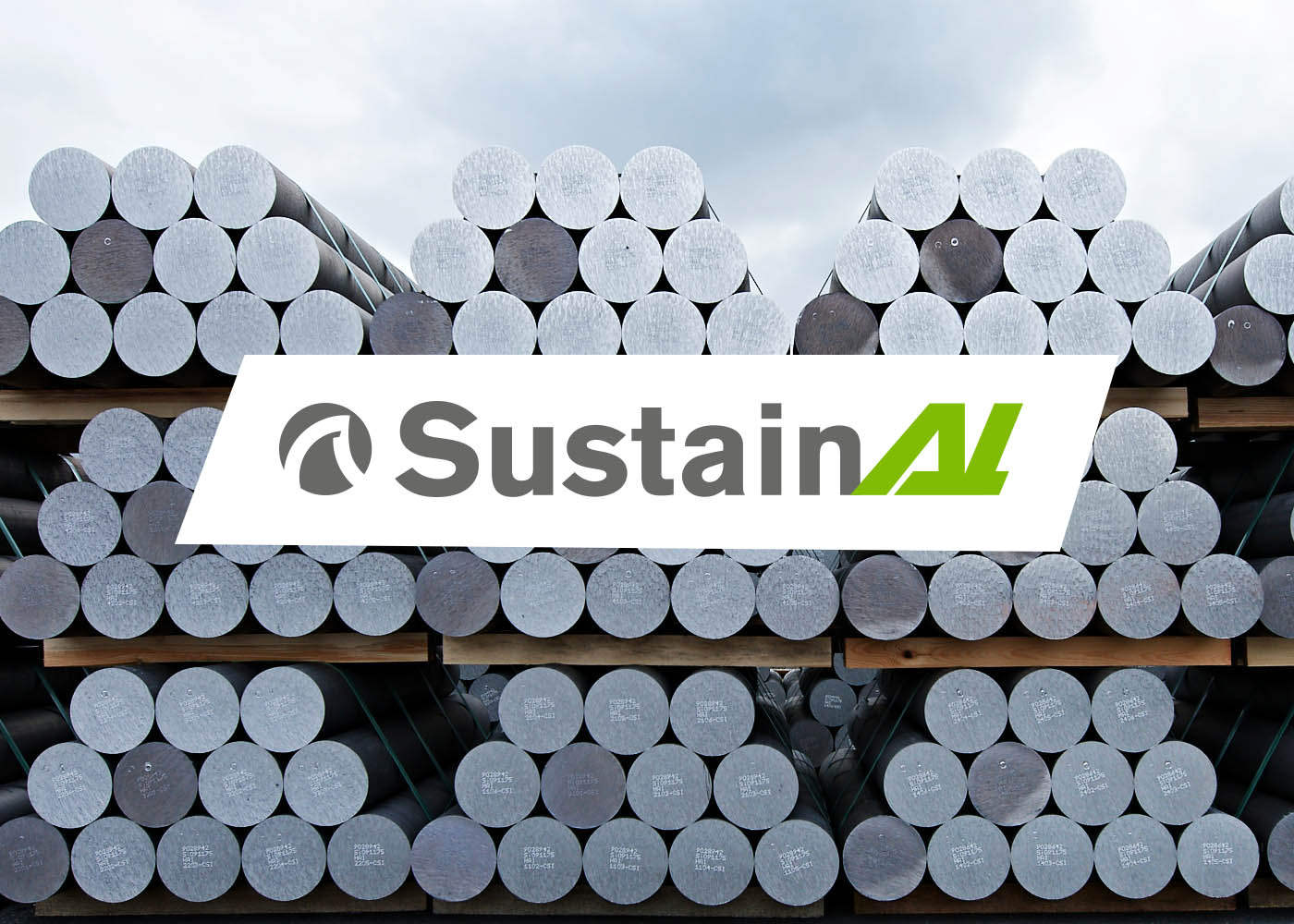
This found that the CO2 footprint of the HAI Standard alloy was 4 to 6 tonnes; for HAI SustainAl 4.0 it was about 4 tonnes, and for HAI SustainAl 2.0 it was roughly 2 tonnes (using an average 80% proportion of recycled materials). HAI is therefore one of the businesses in the sector with the lowest CO2 emissions.
Proof of our sustainable actions
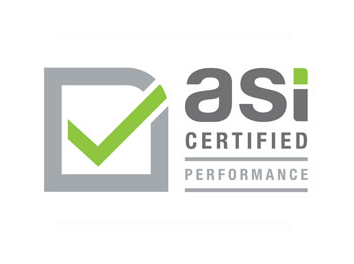
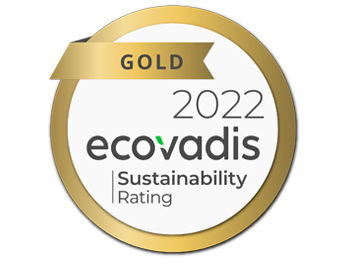
awarded by Ecovadis sustainability rating
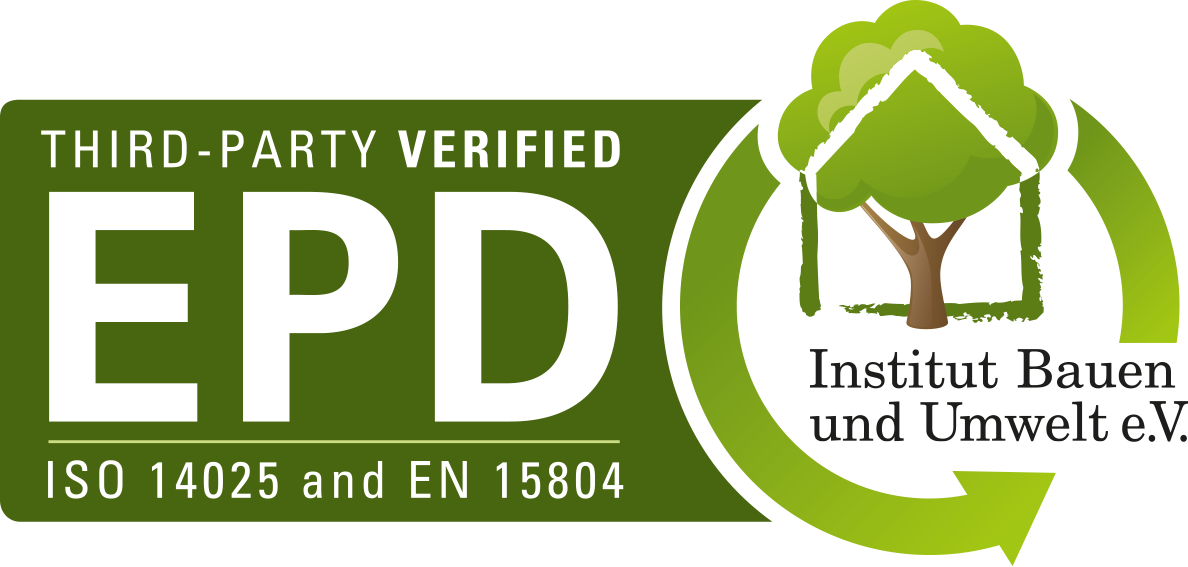
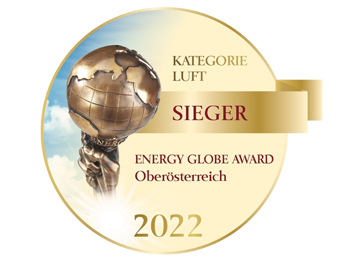
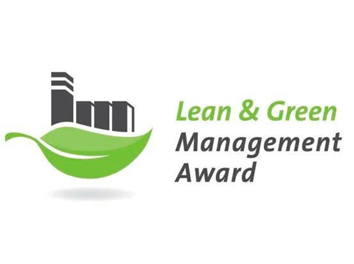
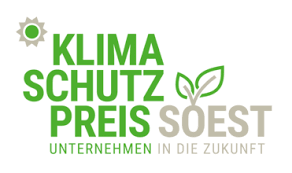
We have exemplary industrial sustainability policies –
HAI sustainability best practices
Would you like to find out
more about our sustainability strategies?
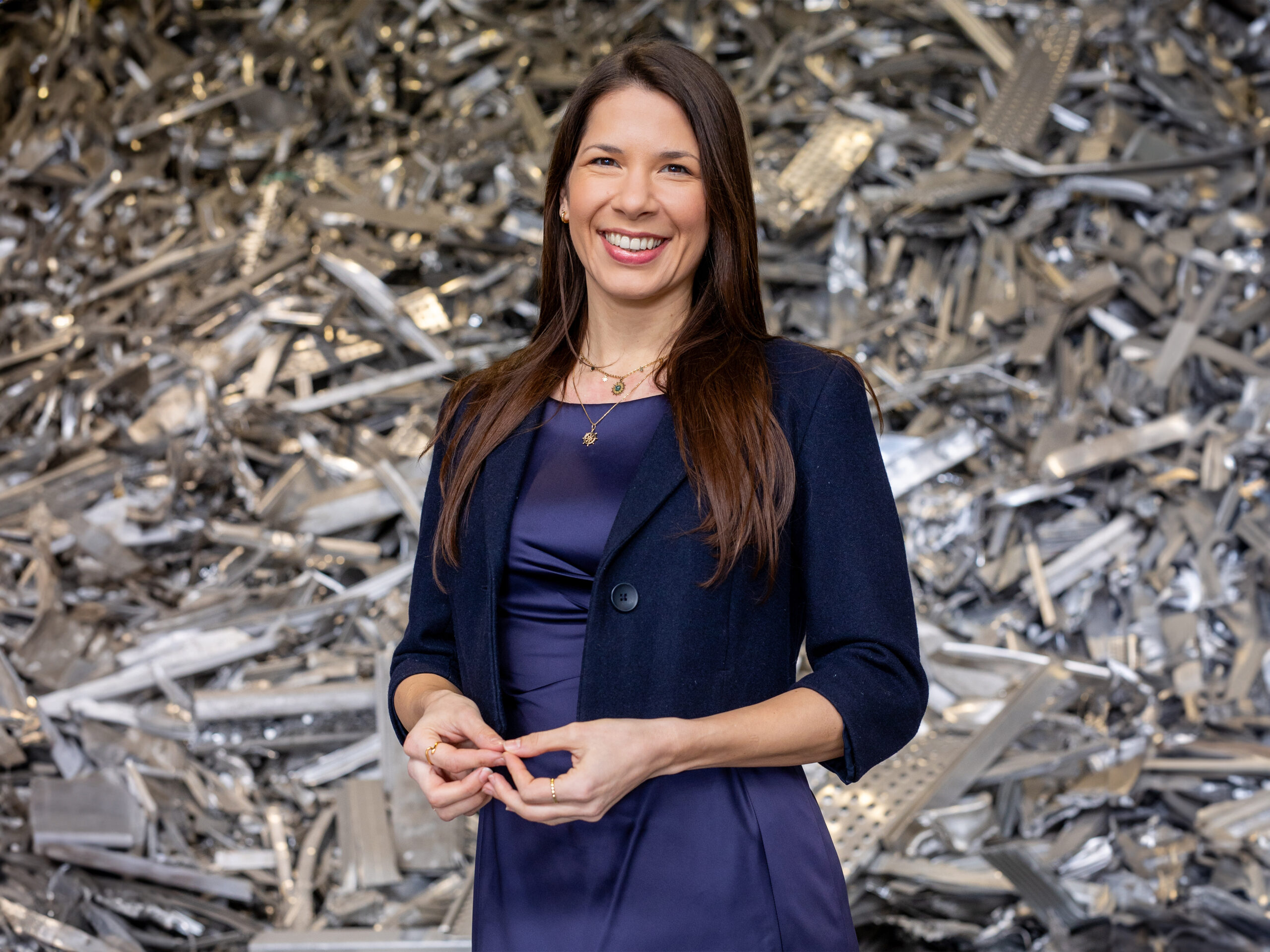