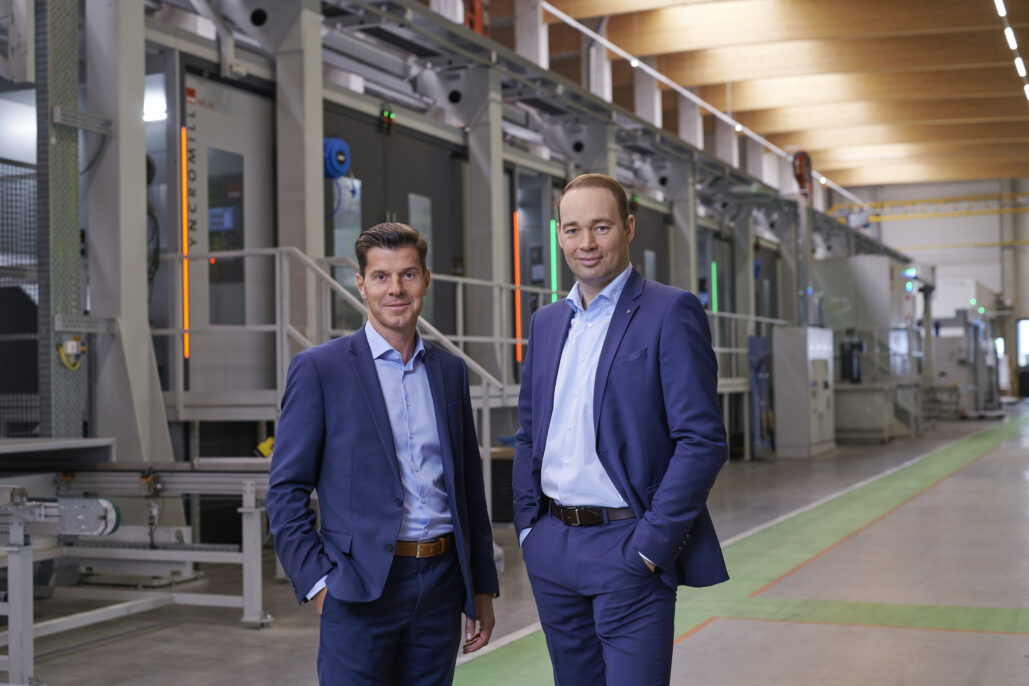
HAI Group invests 125 million euros in sustainable aluminium production and expands its leading role
The European aluminium industry has been struggling with adverse conditions at every turn for some time now. Although aluminium can be found in all sectors, the construction and automotive industries are the major customers of the Austrian aluminium specialist Hammerer Aluminium Industries, and both sectors are not doing particularly well at the moment. In addition to the difficult conditions in Europe, the company is also facing increasing competition from importers from third countries. Despite the difficult waters, HAI believes in the future of aluminium and the necessity of this material for the implementation of the Green Deal. Thanks to its outstanding properties and with regard to sustainability, the company is positive, at least in the medium term.
Fit for the future through investment
The broad strategic focus and the will to shape the future encouraged the management of the HAI Group to launch a 125 million investment package at the end of 2022. All planned projects in this package of measures were completed in the spring of this year.
At the site in Cris, Romania, investments were made in a new 40 meganewton extrusion line with the associated infrastructure, significantly expanding production capacity. Production in Cris is geared towards high-quality products for the solar, construction and industrial sectors. Since taking over the site with 200 employees in 2019, the team in Cris has almost doubled to its current level of almost 400 employees.
Following the successful commissioning of the 40 meganewton extrusion line at the Romanian site in Cris, a 61 MN extrusion line has now also been put into operation in Ranshofen. In recent years, the HAI Group has developed into the technology leader for aluminium components for the transport sector at the Ranshofen site. In particular, lightweight components for e-mobility are produced here. The new plant produces highly complex aluminium profiles with outstanding crash properties for all well-known OEMs in Europe. The new 14,000 m² state-of-the-art logistics center in Ranshofen with a hall, warehouse and loading area is now fully operational and will be officially opened on 12 June. Several trucks can now be loaded and unloaded in parallel in the loading area. A high-bay warehouse is available for customer load carriers, in which goods can be automatically stored and retrieved.
Additional major investments were also made at the German site in Soest. With the construction of a 2,600 m² production hall, additional space was created for the intensive further processing of the products extruded at the site into ready-to-install components. With modern CNC systems and various assembly systems, the production capacities for automotive manufacturers were expanded and space was created for further expansion. The strong growth at the Soest site also required the construction of a new administration building including a new canteen and customer center.
With these expansions, HAI now operates 13 extrusion presses with an annual capacity of 140,000 tons. Together with an annual recycling and casting capacity of 250,000 tons, the aluminium group underlines its leading role in the aluminium industry with its comprehensive production capacities. The company’s commitment to quality, innovation and sustainability is evident at all of its operating sites, which today employ around 2,100 people in the areas of casting, extrusion and processing in Austria, Romania, Germany, Poland and soon also in South Korea. The ground-breaking ceremony for the first non-European plant was held in Gumi/South Korea in April of this year. Together with LS Cable & System, HAI is investing in a company in South Korea. With an investment volume of around 46 million euros, a 13,800 m² production hall including a 60 MN extrusion line for the production of aluminium components will be created. From 2025, the HAI Group and LS Cable & System will produce aluminium components for electric vehicles for the South Korean market at the Gumi site.
Ambitious sustainability strategy
One of the HAI Group’s declared goals is to continuously increase the sustainability of aluminium products through constant innovation. HAI has been involved in the circular economy and recycling processes since the company was founded in 2007 and can therefore count itself as a pioneer in the European aluminium industry. CO2 emissions are well below the European average and a fraction of the global figure. As early as 2019, a conscious decision was made to take measures to reduce greenhouse gases and the target of saving 25% of Group emissions by 2025 was already achieved in 2022 and even significantly undercut.
HAI has been preparing life cycle assessments to evaluate its products since 2020. The decarbonization targets are being achieved by implementing a large number of individual measures. Sustainable corporate management, aluminium recycling, green sourcing and green energy as well as environmentally friendly processes form the pillars for this. With its SustainAl alloys, which have a high recycled content, HAI offers its customers a “green” alternative to existing standard alloys.
The ambitious sustainability strategy makes HAI a pioneer in lightweight aluminium construction. By using an average of 80 percent recycled material and primary aluminium from certified production, which is generated entirely with electricity from renewable energies, the company is a pioneer in climate protection. “Our customers are pursuing ambitious emissions targets. “With our aluminium products, we are a strong partner in achieving these targets – in all three sales areas – transport, industry and construction,” says HAI CEO Rob van Gils, underlining the Group’s sustainable focus.
Alloy variants SustainAl 2.0 and SustainAl 4.0
HAI’s commitment to sustainable performance has resulted in sought-after products. Since the beginning of 2021, HAI has been offering customers the opportunity to make a significant contribution to sustainable production in a simple and transparent way with the SustainAl 2.0 and SustainAl 4.0 alloy variants, in line with European climate targets. “The surface quality properties and mechanical parameters of the alloys are in line with our classic products,” explains Markus Schober, COO of the HAI Group, who has been involved in decarbonization and the circular economy at HAI for many years. The carbon footprint of the SustainAl 2.0 and SustainAl 4.0 alloys is well below the European average. Customers receive certificates for the tons of CO2 saved with SustainAl per project compared to the European or global average or over the desired period. This means that even customers who do not cover their entire aluminium extrusion requirements with SustainAl can evaluate and market individual projects or simply and transparently demonstrate a contribution to their sustainability strategy.
Convincing eco-balance
As demand for the new alloys is constantly growing, HAI has drawn up a life cycle assessment (LCA). According to this, the CO2e/to aluminium billet for the HAI Standard alloy amounts to approx. 4 to 6 tons, for HAI SustainAl 4.0 to max. 4 tons and for HAI SustainAl 2.0 to max. 2 tons. HAI uses up to 80% recycled material for HAI SustainAl 2.0. HAI SustainAl 4.0 uses billets from selected external suppliers as well as its own aluminium billets. This allows HAI to offer its customers sustainable products that have no technological disadvantages. “The entire capacity of both foundries can be used for the production of sustainable alloys. We achieve the high availability by using process and old scrap,” explains Markus Schober. HAI does not promise a solution with a very high proportion of old scrap, which is then hardly available or only in small quantities. On average in the EU, only 10-20% of the recycling material is old scrap. “We are convinced that sustainable aluminium alloys must also be about high availability and an honest, reliable product. This is what our customers expect and it is precisely this solid, sustainable solution that we can deliver with SustainAl 2.0 and SustainAl 4.0,” adds Markus Schober on the HAI strategy. HAI is also going green when it comes to the primary aluminium used. HAI has concluded a supply contract with a partner for 150,000 tons of aluminium over a period of five years and thus has a primary product available that is produced 100% with energy from renewable sources.
The Digital HAIway
In order to ensure optimal structures for future growth and innovation, HAI has been focusing on a digitalization offensive for several years, in which all processes along the value chain are strengthened and optimized. “We see digitalization as an opportunity to maintain product quality and processes at an excellent level. On the other hand, we are focusing on reducing the workload of our employees – digital processes offer great potential when it comes to designing attractive workplaces. However, people are at the heart of all digital projects and digitalization should serve them,” says CEO Rob van Gils, explaining the motives at HAI.
The HAI Group
Hammerer Aluminium Industries employs 2,100 people. Founded in 2007, the company has its headquarters in Ranshofen, Upper Austria, and eight other locations in Germany, Romania and Poland. HAI looks back on a special success story. Here, the dynamism and innovative spirit of a young company are combined with the experience of a traditional business. In 2022, HAI realised a turnover of 990 million euros in the three production areas of casting, extrusion and processing. The products of the HAI Group can be found in the construction sector as well as in automotive and transport technology, electrical engineering and mechanical and plant engineering.
Media contact:
Elfriede Dicker, Management Assistant & Marketing HAI-Group
Hammerer Aluminium Industries Holding GmbH
Lamprechtshausener Straße 69, 5282 Ranshofen, Austria
0043 7722 891 2540, 0043 664 884 61096
marketing@hai-aluminium.com